Today, I had a high pressure pump not delivering water! The official complaint was: “I am here with a Coleman rep and we can not figure out what is wrong with all the bays! All the bays do not have high pressure rinse.” I asked are you sure it is all the bays…. But what do you expect? LOL 🙂 This Coleman rep should also quit…. He allegedly owns a self serve car wash also? I do not believe it. 🙂 He also asked me know to use a Dixmore remote control…. But it is actually not an official remote. But it is actually worse I believe…. I wrote the directions on how to use the remote on the remote. Maybe I am to harsh? 🙂
So obviously you can do your troubleshooting in whatever order you want. I try to do the easy stuff first. Most of the time I like to go straight to the hardest…. But let’s be honest…. That is the dumbest method!
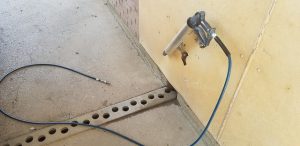
There are quick disconnects in the bays so by removing the gun I can test if there is a clog in the nozzle.
1) Check the nozzle / gun for clogs. Remember a very small amount of dirt or debris can cause the system to not work.
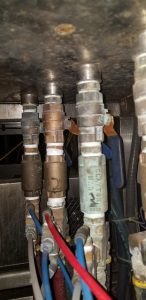
Check your water source to make should you or some random person did not turn it off. I have had this happen before…. By some random person that is…. But I might have done it also? The random person also broken my weep system at least twice. Almost like the random person could care less about my stuff? LOL 🙂
2) Check your water source.
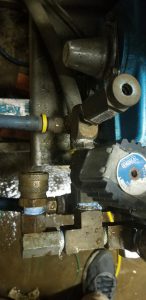
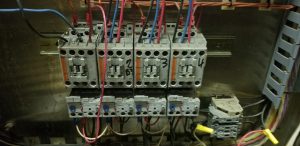
To verify the flow I removed the high pressure hose from the Cat pump…. Then I used the motor starter to see if this fixed the problem.
3) Verify if you are getting high pressure out of the pump.
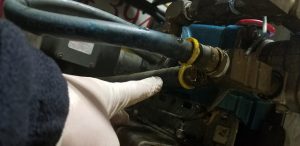
Verify if the water is getting to the pump. (Water should come out of the hose when removed.) I removed the water supply line form the Cat pump to verify this…. I was getting water.
4) Verify if the supply line water is getting to the high pressure pump.
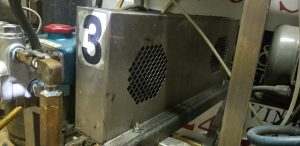
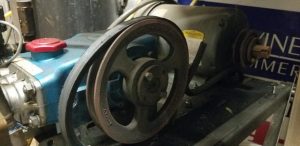
Check to make sure the belt for the motor and high pressure pump is working correctly. This appeared to be my problem…. It actually was not though. I had a different problem which caused this problem. But this will help you troubleshoot most of your high pressure pump problems.
5) Verify that the belt for the motor and high pressure pump are at the correct tension and working correctly.
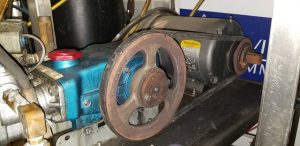
Also when installing a new belt…. I installed mine without removing anything. Try putting the belt on the small pulley and then turning the belt onto the larger pulley.
6) Size matters…. Do not just slam it in there it will not work! Be slow, use your hands and be gentle. This might be something for a different post? 🙂
This would also cover troubleshooting pressure washers.
Tools I used for this repair: LINK
Here is PART 2 on troubleshooting a high pressure pump. LINK